私營鋼鐵企業(yè)推行TPM管理
來源/作者: TPM咨詢服務中心 丨 發(fā)布時間:2017-08-16 丨 瀏覽次數(shù):
日本制造企業(yè)獲得優(yōu)質、低成本和高效率的秘訣除了其獨特的生產管理模式――豐田生產制((Toyota Production System,簡稱TPS)和全面質量管理((Total Quality Management, 簡稱TQM)外,還有一個重要的秘訣是采用全員生產維護(Total Productive Maintenance,簡稱TPM咨詢)。它是制造型企業(yè)降低成本,提高產品質量、擴大企業(yè)的生產能力,增加效益的最直接,最有效的途徑之一。以下淺析私營鋼鐵企業(yè)推進全員生產維修(TPM)理念的八步走。
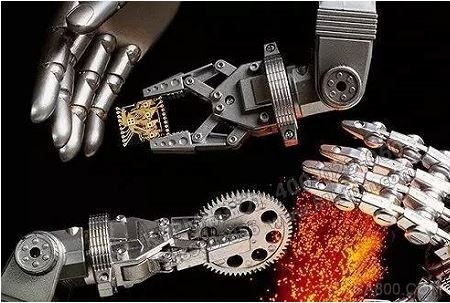
TPM管理
1 現(xiàn)場6s管理
6s是對生產現(xiàn)場各主要生產因素所處狀態(tài)不斷進行整理、整頓、清掃、清潔、素養(yǎng)(人的要素)、安全等一系列現(xiàn)場管理活動。在推進全員生產維修過程中首先實施6s的目的在于打造整潔、有序的生產現(xiàn)場,為推進提供現(xiàn)場保障;同時培養(yǎng)職工嚴謹?shù)墓ぷ鲬B(tài)度,增加員工責任心,以實現(xiàn)減少浪費、提高生產效率的管理為最終目的。崗位工通過對設備進行清掃、擦拭來發(fā)現(xiàn)一些“隱形”問題,如裂紋、松動等,從而守護設備管理的第一道防線。
2 組建專職點檢體系
所謂“點檢”就是按標準,用人的感觀或儀表、工具,定人、定點、定期地對設備進行檢查,掌握設備故障的前兆信息,及時采取對策,消除故障隱患的一種設備管理方法。組建專職點檢體系,即按照一定比例(建議為維修人員總數(shù)的10%)抽調維修人員,成立專職點檢隊伍。點檢人員依照公司制定的點檢標準、潤滑標準對設備進行周期性的檢查,并對崗位人員的點檢工作進行監(jiān)督、指導,作為設備“管家”守護設備管理的第二道防線。
3 劃分產線、尋找狀態(tài)受控點
設備管理是以服務生產為中心導向。因此設備管理的重點是企業(yè)產品作業(yè)線設備,即在生產過程中不可缺少的設備。產品作業(yè)線是由不同數(shù)量的設備組合而成。產線劃分則依據生產工藝特點,本著便于管理的原則進行劃分;點檢部位(點)就是確定設備點檢時的關鍵部位、薄弱環(huán)節(jié);設備易出故障的部位(故障點),即設備易劣化的部位。點檢的目的是對點檢部位(點)狀態(tài)進行控制,所以也稱狀態(tài)受控點。狀態(tài)受控點的尋找途徑為:產品作業(yè)線→找受控(關鍵)設備→到狀態(tài)受控點。受控設備的范圍為:
(1)產品作業(yè)線設備:如高爐、燒結、轉爐等產線設備;
?。?)非產品作業(yè)線設備(或普通作業(yè)線設備):如制氧、供配電、動力等設備;
?。?)其他需預防維修的單機性設備,如天車等設備。其尋找過程應遵循“存在隱患”、“較難修復”、“比較貴重”三條原則。通過對狀態(tài)受控點的尋找,明確各級人員的關注重點,做到精細管理。
4 簽訂“三方協(xié)議”
所謂“三方協(xié)議”具體是指操作方、維修方、點檢方簽訂的點檢維護分工協(xié)議。三方分工協(xié)議是針對產線關鍵設備及狀態(tài)受控點,以協(xié)議方式規(guī)范操作方、維修方、點檢方三方職責,及其對設備維護的內容、標準和主要績效指標,實現(xiàn)三方對設備管控的辦法。如圖1,明確了每臺設備關鍵點檢部位的作業(yè)分工。
5 單體設備總點檢
總點檢是對同一類設備,由設備“三位一體”管控責任體系中的相關人員,對設備上同類型的“點”,集中一段時間盡責盡力地實施點檢。通過大面積的總點檢,檢查設備現(xiàn)狀并作出診斷分析;總點檢的流程為:確定設備類別→制定點檢標準、工具表單→點檢前的教育培訓及演示→啟動儀式的策劃→總點檢啟動實施→領導和專業(yè)人員的巡視→點檢問題和困難源的查找、統(tǒng)計→點檢問題的分類、歸口處理→點檢困難源的研究、歸口處理→點檢檢查與核驗→總結,資料的匯總與存檔→問題處理情況的跟蹤總結與提高。
6 編制四大標準、九項制度
四大標準包括點檢標準(含法定檢查標準)、維修技術標準、給油脂標準、維修作業(yè)標準。其中,維修技術標準是點檢標準、給油脂標準和維修維修標準的基礎,是編制其他三項標準的依據。維修技術標準包括:設備(裝置)的所更換零件的性能構造、列出簡明示意圖及使用材料等;零件的維修特性,包括機件減損量的劣化傾向、特殊的變化狀態(tài)及點檢的方法和周期;設定主要更換件的維修管理值,包括零部件的裝配圖面尺寸、裝配間隙、允許減損量的范圍,以及測定的項目、內容、周期和使用標準等;零件應限制的項目內容,諸如溫度、壓力、流量、電壓、振動值等。點檢標準確定了點檢項目的判定標準:規(guī)定了對象設備的點檢項目、內容、點檢時的設備狀態(tài)、周期、判定標準以及點檢的分工、方法等。給油脂標準明確了給什么品種的油和脂、給油脂的方式、一次給的油脂量是多少、何時給油、誰來執(zhí)行這五大要素。維修作業(yè)標準是點檢員確定檢修作業(yè)流程、工藝、工時和費用的基礎,是檢修作業(yè)的依據。具體內容包括:作業(yè)名稱、作業(yè)方法、作業(yè)的工藝順序、作業(yè)項目、作業(yè)條件、技術條件;安全注意事項、及工器具;作業(yè)人員、作業(yè)時間、總工時等。
設備的九項管理制度及相互關系:(1)設備點檢制度、設備定修制度是主體。(2)設備使用維護制度、設備檢修工程管理制度、設備維修管理制度、設備維修技術管理制度是手段、是條件。(3)設備技術狀態(tài)管理制度(或功能精度管理制度)、設備事故障管理制度、設備維修費管理制度是目標。
7 確定停產檢修模型
開展全員生產維修(TPM)活動就是要及時發(fā)現(xiàn)、及時處理設備的缺陷和隱患,因此可以說點檢是停產檢修的開始、停產檢修是點檢的后續(xù)。兩者是應視為一個整體。停產檢修就是在點檢的基礎上,在主作業(yè)線設備(或對主作業(yè)線生產有重大影響的設備)停機(停產)條件下,按定修模型進行的計劃檢修,一般分為日修、停產檢修、年修、三類,其核心是定修模型的設定。停產檢修模型是公司各產線設備的定修周期、定修時間、定修日(三要點)、工序組合、檢修負荷(兩要素)的綜合平衡設定表。停產檢修模型的作用:
(1)均衡檢修力量,提高檢修效率。
(2)對產線停產定修時間,按生產計劃需求進行迅速調整平衡,仍可按定修周期、定修時間及檢修負荷人數(shù)組織定修,從而實行維修計劃值的有效管理。
?。?)停產檢修模型可為公司原料、生產、運輸、能源安環(huán)等計劃編制提供依據。
(4)合理科學的模型,能達到適時修理,確保設備正常運行,避免事故,減低維修費用。
企業(yè)設定停產檢修模型的依據為:
?。?)公司經營方針和經營規(guī)劃;
?。?)公司設備維修方針和維修策略;
?。?)設備前期的運行狀態(tài)與模型運作實績;
?。?)生產物流、能源介質和檢修人力資源平衡;
?。?)同類企業(yè)的管理水平。停產檢修模型屬于動態(tài)型的檢修管理模式,模型需要在實踐中不斷完善和優(yōu)化。
8 固化提升
通過以上努力,雖然會取得一定的成果,但全員生產維修推進過程是一個持續(xù)改進、永無止境的過程,因此固化提升也是至關重要的。因此需要通過加強員工的自主管理活動來實現(xiàn)固化提升。具體措施有:
(1)在點檢站開展制作、培訓單點課活動,通過單點課的制作與培訓,可以加快點檢人員相關業(yè)務水平的提高,同時能夠使崗位人員更加直觀的學習到設備的維護、點檢等方面知識。
?。?)征集各分廠的自主改善成果并進行相應的獎勵。自主改善成果是員工或攻關小組針對現(xiàn)場存在的問題提出解決方案,組織實施并得到的有益成果。其主要包括在日常生產中涉及到的安全、設備、成本、倉儲、環(huán)保、現(xiàn)場定置、能源等方面內容。通過調動員工參與技術改革、開拓創(chuàng)新的積極性,充分發(fā)揮廣大員工的聰明才智,保證各項改善工作的有效實施,提高全廠的綜合效益。
?。?)加強“六源”的排查。“六源”包括污染源、清掃困難源、故障源、浪費源、缺陷源、危險源。通過對員工查找、處理現(xiàn)場“六源”問題并及時反饋“六源”整改情況進行判定,對于整改后成效顯著的進行相應的獎勵,以保證“六源”管理工作規(guī)范化、常態(tài)化。
本文素材均來自網絡,如有侵權請告知刪除。
- 上一篇:85個知識點全面解釋TPM
- 下一篇:IE與TP(TPM)的結合